DESIGN, FABRICATION & INSTALLATION OF PLASTIC STORAGE WAREHOUSE
Red Leaf Enviro were contacted by enVar to design and install a new light plastics warehouse within one of their recycling facilities in St Ives
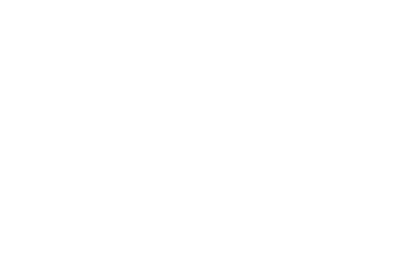
CLIENT
enVar the UK’s largest waste in vessel and composting facility, processing over 100,000 tons per year
PROJECT
Design and installation of a new materials storage warehouse for light plastics, situated within a recycling warehouse
14×9
METRES
WAREHOUSE SIZE
5
METRES
WAREHOUSE HEIGHT
10
DAYS
TO COMPLETE
enVar run a busy materials recycling facility in St Ives, processing a range of materials including light plastics. As part of the process, once sorted, light plastics would be vacuumed from a piece of MRF plant into an uncontained area. This was causing efficiency problems for the site as these small light plastic pieces were easily disturbed by air movement and the load shovels used to collect the plastic would sometimes struggle to load up these plastics into their bucket.
Red Leaf Enviro were contacted to provide a suitable containment area within the facility to store these plastics, along with providing a solution to the collection of these plastics, using plant. The Red Leaf Enviro team developed a steel and concrete shed design that would contain the plastics and allow the load shovels to enter the shed and use concrete walls as a barrier to push the light plastics against while loading.
While the design of this storage shed was completed at Red Leaf HQ, the fabrication of the steels for the project was to be done on site, due to difficulties with accessing the site with wide or long loads.
To begin, the steel framework was erected next to the exit point in the material recovery line for the light plastic pieces, the erection required the steels to be concreted into the ground below to ensure they were held in place. Once the steel work had been erected, concrete panels were inserted into three sides of the steel framework up to two thirds of the height of the building, the concrete panels sit within the steel framework as well as being bolted to the steels, to provide extra security.
Cladding was then added to the roof and the entrance to the building, large clad doors were also hung to provide access for the load shovellers when required. A mesh was fitted to the top third of the building to allow free movement of air out of the building while plastics were being vacuumed in from the material recovery line.
Once completed the building could be filled with light small plastics from the recovery line and keep them contained on site until their removal. The removal of the plastics was also made easier by the wide doors and concrete walls; allowing the load shovellers to enter the building and use the concrete walls as a stop when loading the plastics.
Contact Red Leaf Enviro
to discuss your project
Contact us today to discuss the requirements of your next project, our experienced team will be happy to help.
We can provide a full turnkey solution or fabricate and install to a third-party design.